The hot-dip galvanizing process is a widely used technique in the metallurgical industry for protecting metallic materials, such as aluminum and steel, against corrosion. This surface treatment involves immersing sheets, metal meshes, or other elements in a molten zinc bath, ensuring a completely coated and protected surface from the corrosive effects of the environment.
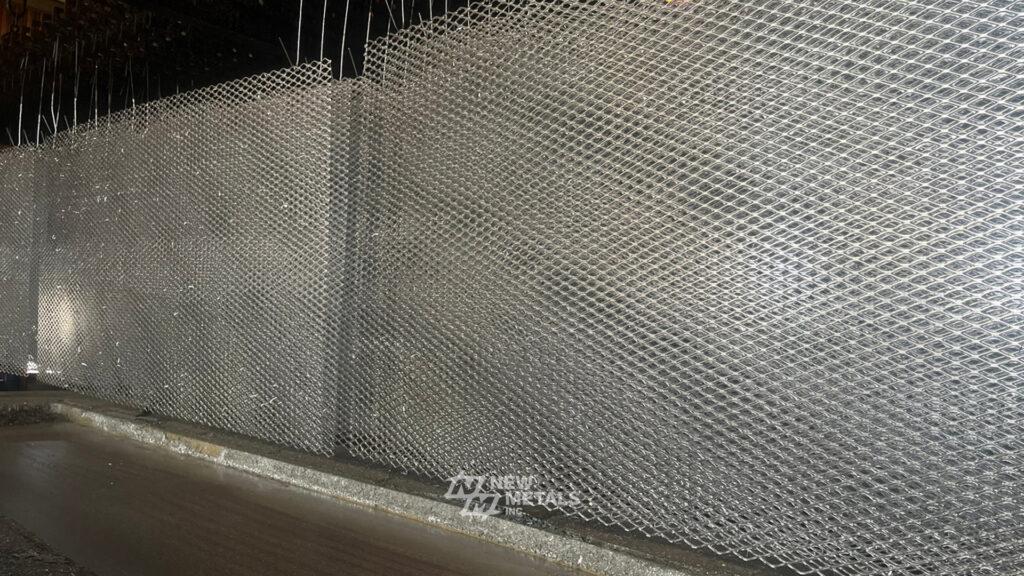
Main Steps of the Hot-Dip Galvanizing Process
Hanging: The metal pieces to be galvanized are hung on special structures to facilitate their immersion in the zinc bath.
Pickling: The pieces undergo a cleaning process using acids to remove oxides, grease, and other contaminants present on the metal surface.
Rinsing: The pieces are rinsed with water to remove any residue from the acid used in the pickling process.
Fluxing: The pieces are submerged in a flux solution containing zinc salts to remove residual oxides and promote better zinc adhesion during the galvanizing process.
Drying Oven: The pieces are introduced into an oven to dry and remove any traces of moisture before being submerged in the zinc bath.
Galvanizing: The pieces are immersed in a molten zinc bath, where the zinc adheres to the metal surface, forming a protective layer.
Inspection and Details: The galvanized pieces are inspected to ensure the quality of the coating and additional details are performed if necessary.
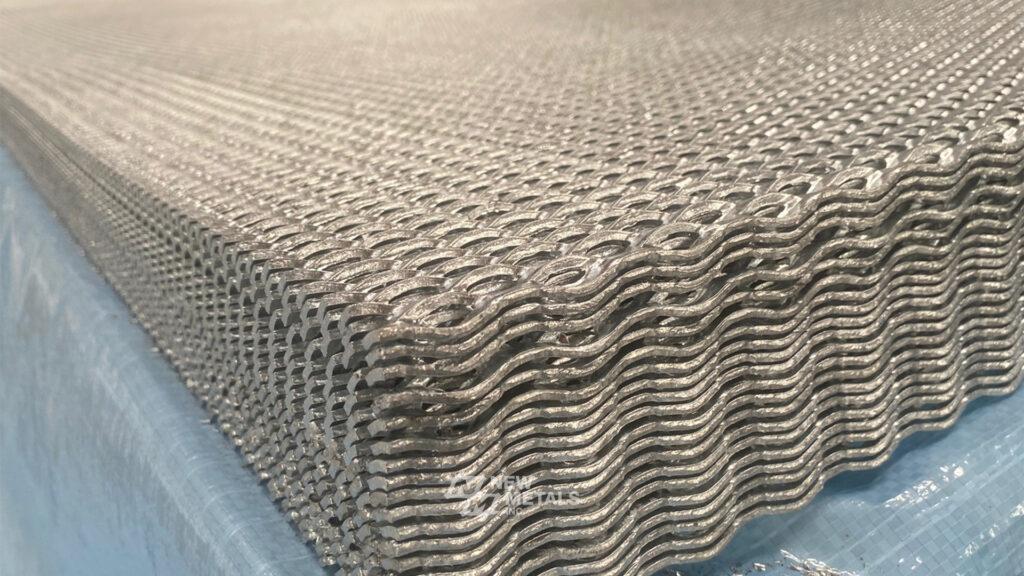
Advantages of the Hot-Dip Galvanizing Process
Hot-dip galvanizing offers several advantages compared to other techniques, such as electroplating and electrogalvanizing. It is more economical, does not require expensive equipment, and allows for the manufacture of large quantities of materials.
Types of Hot-Dip Galvanizing Processes
There are two hot-dip galvanizing processes: Batch and Continuous.
Batch: In this process, the already manufactured steel pieces are submerged in the zinc bath. The dimension of the pieces is limited by the size of the zinc vat. During the process, a metallurgical bond is formed, ensuring strong adhesion of the zinc coating, superior to other forms of coating.
Continuous: This process is used to galvanize steel sheets destined for the automotive industry, white goods, and civil construction in general. The process is essentially the same as Batch but operates continuously. A steel coil is unwound and goes through the entire cleaning and galvanizing process. At the end of the process, it is rewound.
Applications of Hot-Dip Galvanizing
The hot-dip galvanizing process is applied in various sectors, such as construction, automotive, and white goods, due to its anti-corrosive characteristics and adhesion properties. Some common applications of hot-dip galvanizing include:
Steel structures: Hot-dip galvanizing provides excellent corrosion protection for steel structures, such as bridges, electrical transmission towers, industrial and commercial buildings, and street lighting poles.
Automotive industry: Steel parts used in vehicles, such as chassis, brackets, and suspension components, are often hot-dip galvanized to enhance their corrosion resistance and extend their service life.
White goods: Household appliances like washing machines, dryers, refrigerators, and stoves often include galvanized steel components to protect them from corrosion and ensure greater durability.
Public infrastructure: Elements such as railings, benches, and trash cans in public spaces can also be hot-dip galvanized to protect them from corrosion and ensure their longevity.
Agriculture: Agricultural equipment and machinery, like irrigation systems, silos, and greenhouse structures, benefit from the hot-dip galvanizing process as it provides protection against corrosion in damp and outdoor environments.
Maritime industry: Hot-dip galvanizing is essential in maritime and coastal applications, where exposure to saltwater and moisture leads to a high rate of corrosion in metallic materials. Components such as anchors, chains, and boat fittings are galvanized to ensure a longer lifespan and resistance to corrosion.
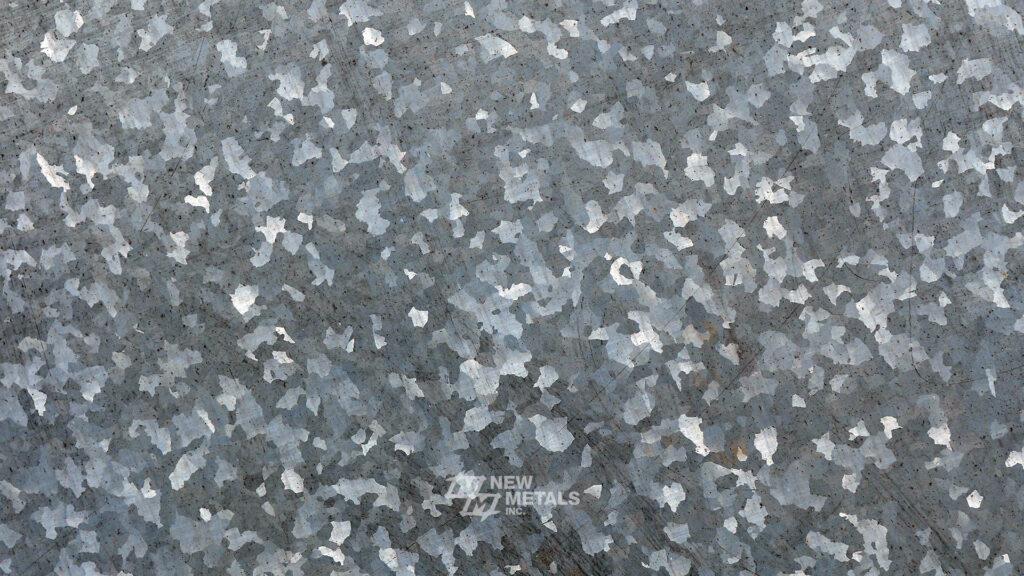
In conclusion, the hot-dip galvanizing process is a widely used technique in the metallurgical industry for protecting metallic materials against corrosion. By immersing pieces in a molten zinc bath, a completely coated and protected surface from the corrosive effects of the environment is ensured. With two main methods, Batch and Continuous, hot-dip galvanizing offers economical and efficient solutions for a wide range of applications and sectors.